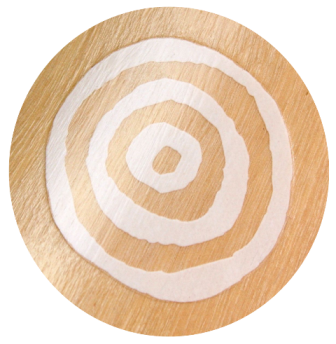
French manufacturer of "Kurungaï" didgeridoos
Who am I?
My name is Gregory Zwingelstein, and yes I am the ' daddy ' of Didgeridoo Passion. I am finally back in the instrument making business! Since 2010 I have been mixing my passion for the didgeridoo and woodworking to provide after-sales service for each instrument and to (for example) make custom mouthpieces. At that time, I was already making a few instruments. I learned with the Aborigines in Australia the traditional way of making yidakis, and in the past organized multiple manufacturing courses with Bruce Rogers.
All these experiences and the hundreds of didgeridoos from different horizons have allowed me to understand how to use the resources of Australian nature, and get the most out of a termite eucalyptus trunk. The trunks I use are mostly collected generally in autumn, when the sap is not active in the trees. They are cut under the authorization of the state government. Before being worked they dry for at least 6 months.
How do I make my didgs?
I want to immediately clarify that I do everything by hand, really! Because in my manufacturing philosophy, the only way to "give birth" to a didgeridoo is to follow by hand (with a plane, and especially a spokeshave) the different layers of the eucalyptus growth. To know when to stop or when to make more shavings. A manual job that takes a lot of time, both in the internal and external manufacturing phase as well as in the finishing phase... So I start with a trunk ranging from 10 to 15kg to produce a didgeridoo between 3 and 4kg...
Concerning the mouthpieces, I make for each instrument a mouthpiece made of wood such as ash, elm, pear, walnut, boxwood or others in order to ensure optimal comfort but especially the stability of the instrument. For the interior treatment, I use ecopoxy resin (high quality bio-sourced epoxy resin) to ensure the stability of the instrument over time. I inlay a boulder opal in each instrument in the place that seems most judicious to me, often where the didg has a hole in the formwork or where termites have made a ventilation hole. And for the exterior finish, I use a hard oil in several layers in order to obtain a more natural and satin finish, far from the epoxy finish which is too glossy for my taste.
What does my logo mean?
I did not choose this logo by chance, it has several meanings but the main one is gathering.