History & manufacturing
The Australian bush...
Among the Aborigines, the didgeridoo player accompanies the singer and the dancer during the various ceremonies (initiation, death, etc.). He then tells a story, the story of which he is the guardian. He reveals it only in ceremonies in the presence of initiates. Thus each Aboriginal person is responsible for his or her history passed down by their elders and which they must pass on to the next generation. The whole thing forms what they call Dreamtime, their mythology. The didgeridoo played by Aboriginal people in northern Australia is called " traditional didgeridoo ", while the didgeridoo played by Western players is called " contemporary didgeridoo ".
As for the word " digeridoo ", it was invented by white people when they discovered the instrument. Indeed, the colonists heard a strange sound which they transcribed with the word “digeridoo”. The Aborigines have several ways of naming it, which vary depending on the places where it is played, but two names are often cited: Yidaki (Yirrkala region) and mago (Maningrida region) . They are both made using traditional methods, by an experienced Aboriginal from Arnhem Land and usually painted with the clan's designs.
In the ancestral footsteps of the didgeridoo: where exactly does it come from?
What often makes the difference between a yidaki and a didgeridoo is the configuration of the air column hole. The interior of a yidaki is very often narrower than a didgeridoo and very little worked. We obtain a raw and compressed sound, resulting in a very responsive instrument with easy-to-reach hoots.
Steps in Making a Didgeridoo by Bruce Rogers (tribute to this wonderful Australian Didgmaker):
Raw eucalyptus trees are all termite (naturally dug by termites) and cut under state government permission. Bruce was careful to only cut down the trees he was going to use. The wood is then stored in a special room with regulated ambient conditions for one year. |
An important moment, giving the didge its individual note and characteristics. a) Bruce tunes each didge by shortening the wood. Different shapes and lengths produce different sound qualities, and the cuts highlight the best of what nature has provided.
b) The cavity dug by the termites is accentuated to obtain a bell and refine the tuning. |
Here, Bruce removes the bark from the wood. The trunk dried after cutting for twelve months. This eucalytpus is a Messmate-Stringybark (Tetrodonta eucalyptus). |
Excess wood is planed from the outside to reduce its weight and improve resonance. Bruce used hand tools and reduced the wall thickness gradually until the didge began to “sing”. |
Bruce used several grades of sandpaper to smooth the exterior. Finally, a clear varnish gives protection and increases the beauty of the wood. A mouthpiece is fitted and the didge is numbered. Here is the instrument ready to play! |
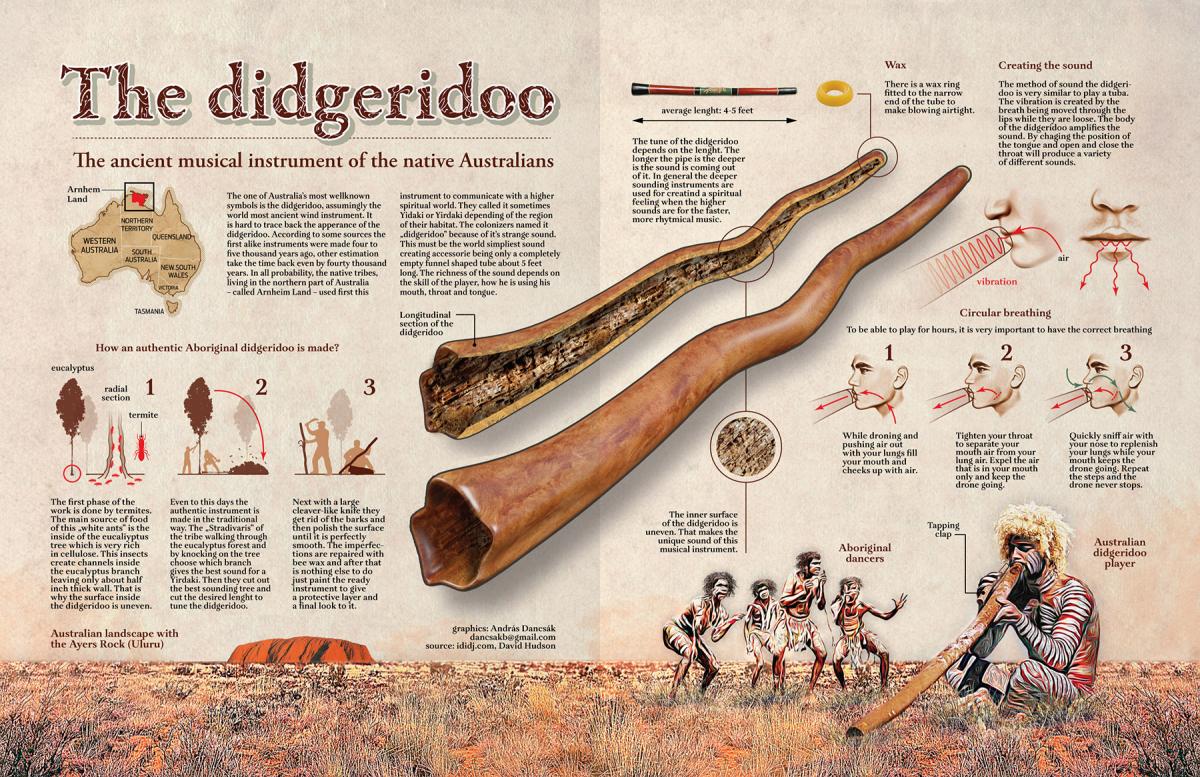